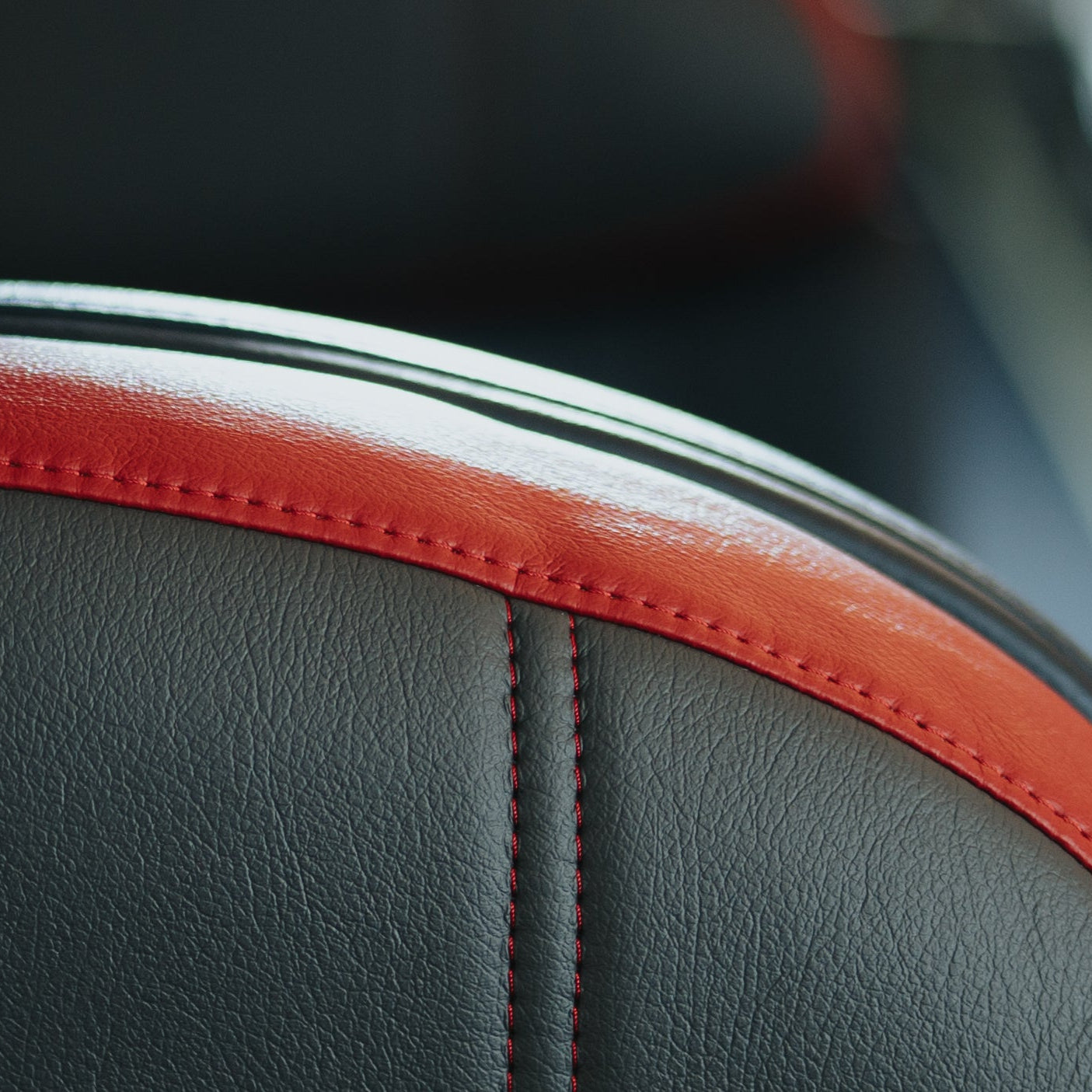
Why Generation Global?
Generation Global stands out by providing turn-key solutions that make changing your aircraft interior seamless and hassle-free. Our reputation for fast and efficient certification ensures your projects are completed on time and on spec.
Choose Generation Global for comprehensive, ready-to-use solutions with global reach.
Cover Production
Generation Global have large scale cut and sew production facilities for manufacture of dress covers and accessories.
Capabilities including perforation, embossing, debossing, quilting and embroidery allow endless customization options for clients.
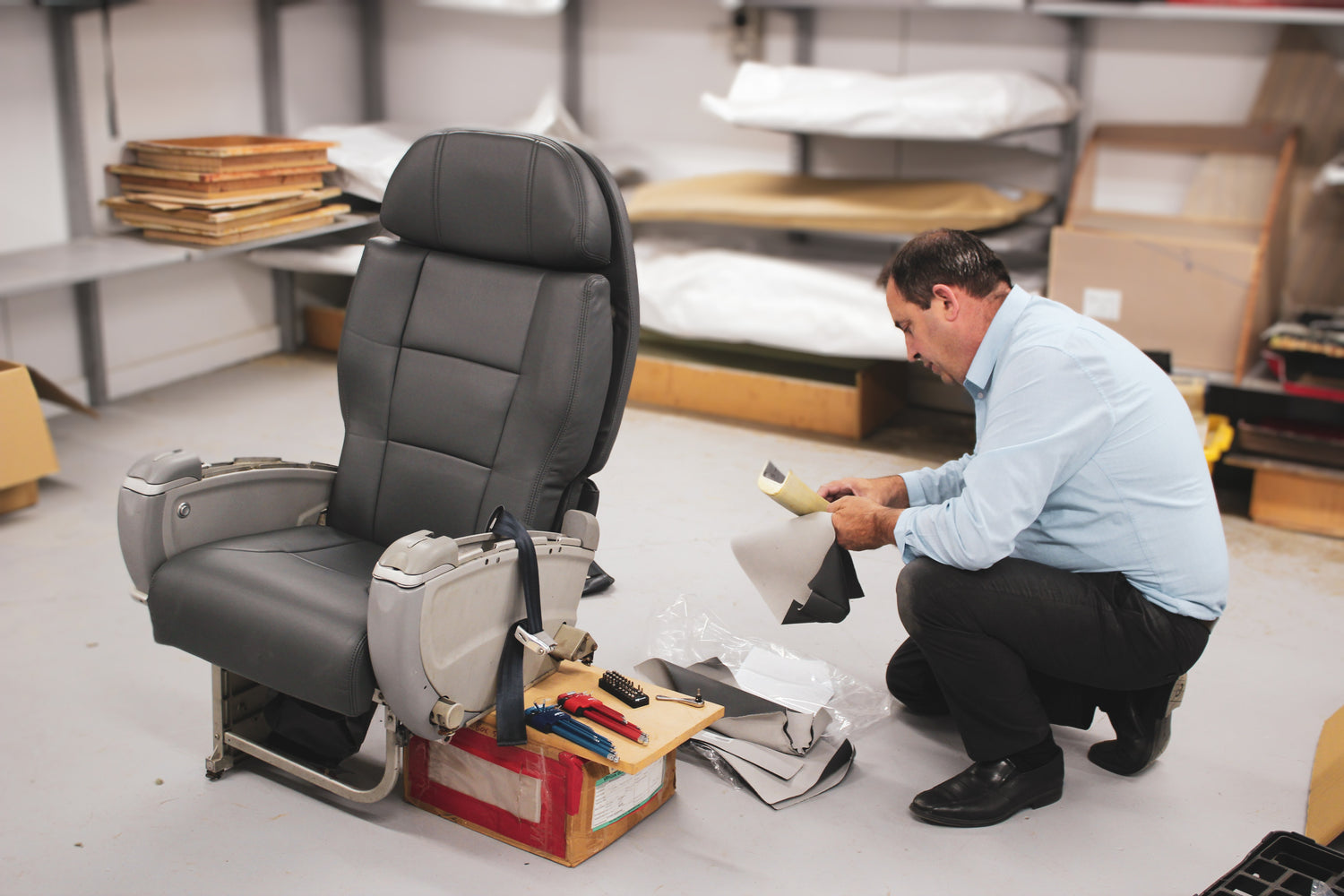
Prototyping & Development
Our prototyping process involves several key steps. First, we carefully assess the existing interior components to understand their design and fit, then using advanced techniques we reverse engineer old covers to create accurate prototypes, the protypes are then fitted to seats to check for any adjustments needed.
Once prototypes are perfected, we move on to a full-scale production and installation.
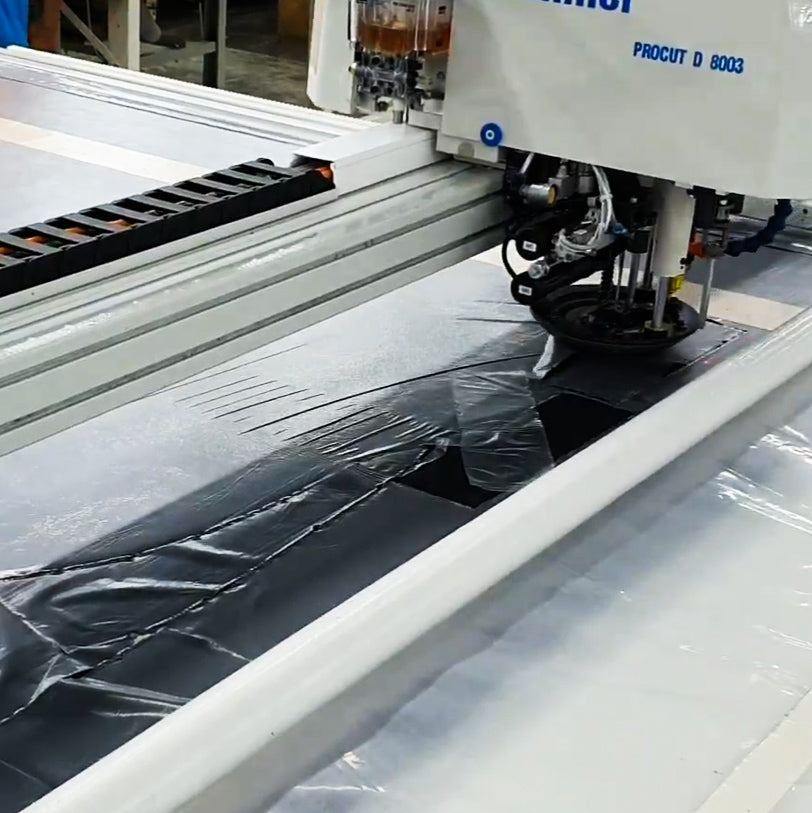
CNC Cutting
CNC (Computer Numerical Control) cutting for airline dress covers is a precision-driven process that uses automated cutting machines to fabricate seat cover materials with high accuracy and efficiency. This method ensures uniformity, reduces material waste, and enhances production speed compared to manual cutting. CNC cutting is ideal for handling various fabrics, including leather and synthetic textiles, ensuring consistent quality and fit for airline seat covers while meeting industry standards for durability and aesthetics
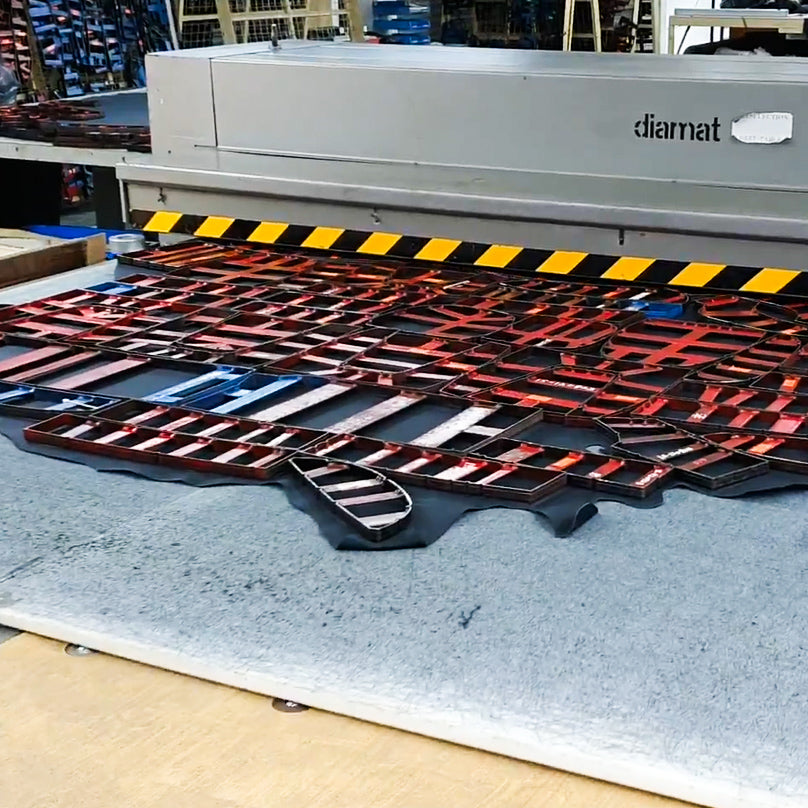
Press Bed Cutting
Press bed cutting for airline dress covers is a traditional method that uses a hydraulic or mechanical press with a die (custom-shaped blade) to cut fabric materials. This process is efficient for high-volume production, ensuring consistency in shape and size. It is particularly effective for thicker materials like leather or multi-layered fabrics, offering durability and precision.
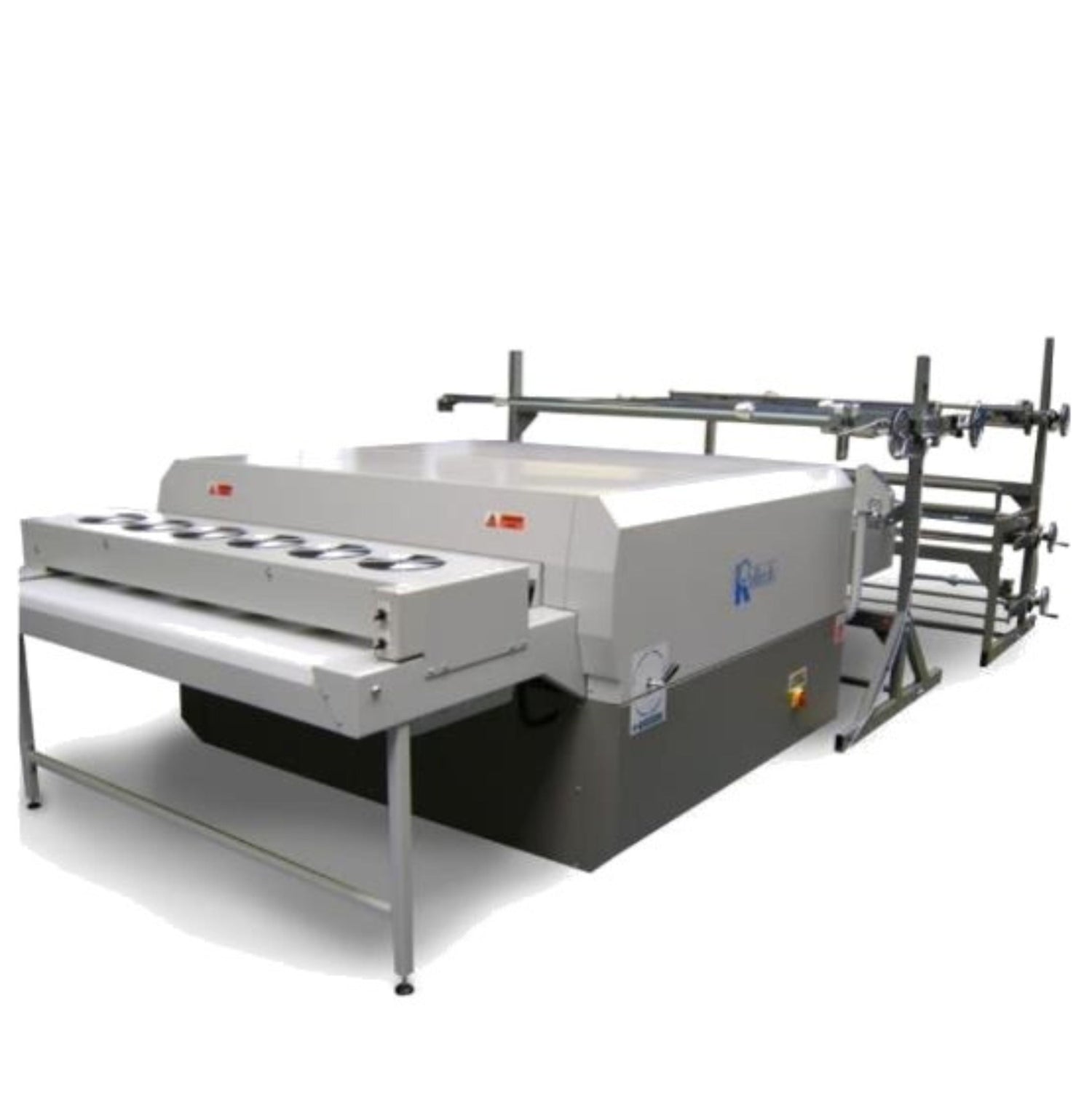
Lamination
Lamination for airline dress covers involves applying a protective or reinforcing layer to the fabric to enhance durability, comfort, and aesthetic appeal. This process can include heat, pressure, or adhesives to bond materials like foam, film, or non-woven backing to the dress cover fabric. Laminated covers improve resistance to wear, stains, and fire while maintaining flexibility and breathability. This is particularly important for meeting aviation safety standards and ensuring a premium look and feel for airline seating.
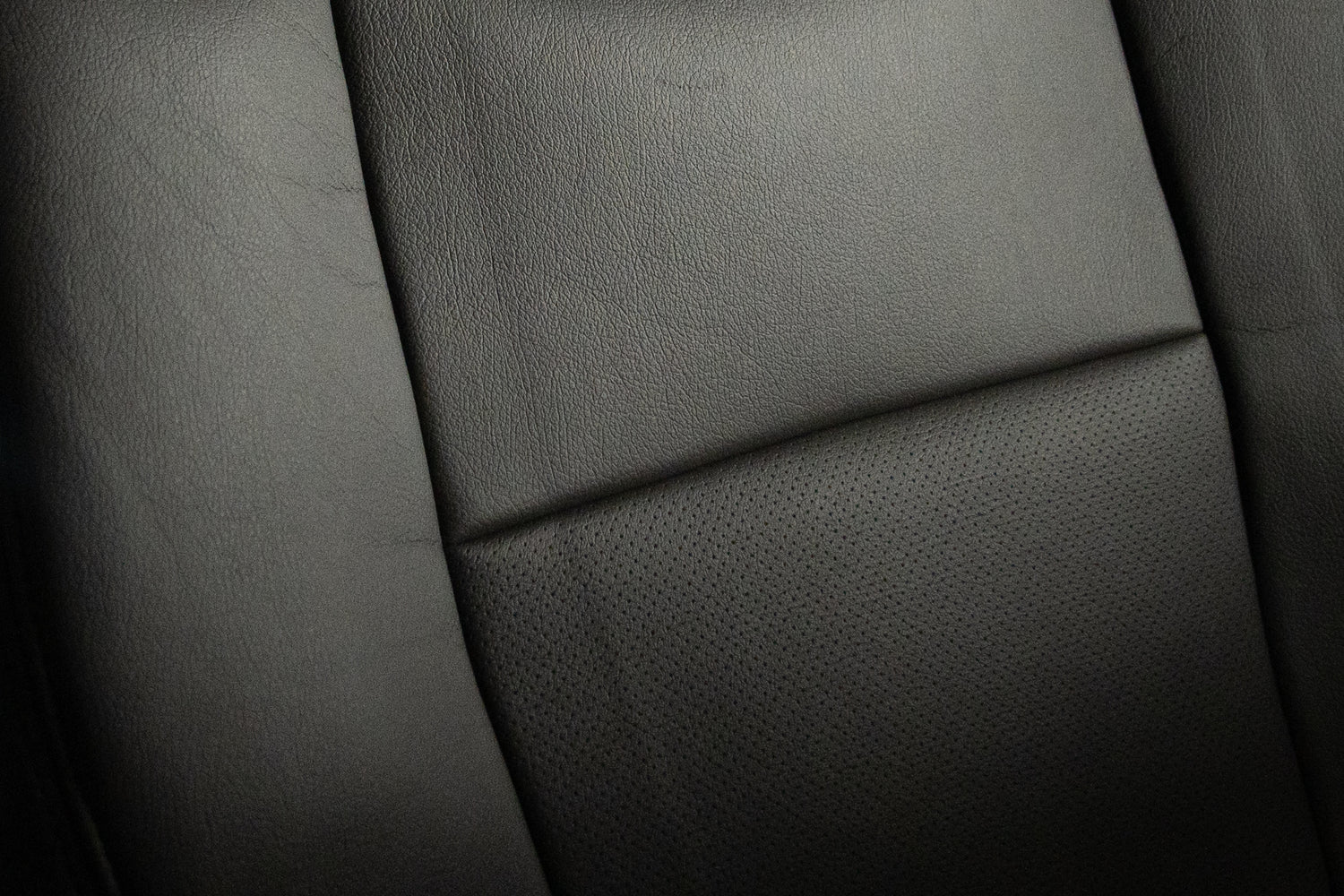
Perforation
Perforation on airline dress covers involves creating small, evenly spaced holes in the fabric to enhance breathability, comfort, and aesthetics. This process is commonly used in leather or synthetic materials to improve airflow, reduce heat buildup, and provide a more comfortable seating experience for passengers. Perforation can also contribute to the overall design and branding of the airlineβs interior while maintaining compliance with aviation safety and durability standards.
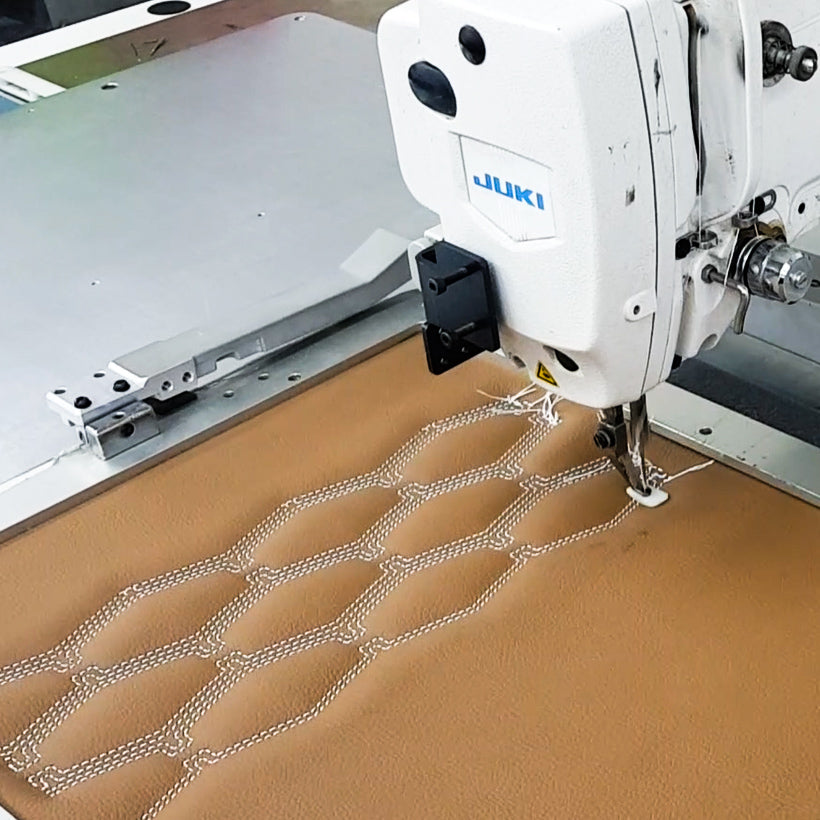
Computer Quilting
Computer quilting for airline dress covers is a precision stitching process controlled by automated quilting machines. It allows for intricate and consistent patterns to be stitched onto fabric layers, enhancing both aesthetics and functionality. This method improves seat cover durability, provides additional cushioning, and can be customized with unique designs or branding elements. Computer quilting ensures uniform stitching quality and is commonly used with materials like leather, synthetic fabrics, and laminated textiles to meet aviation industry standards for comfort and longevity.
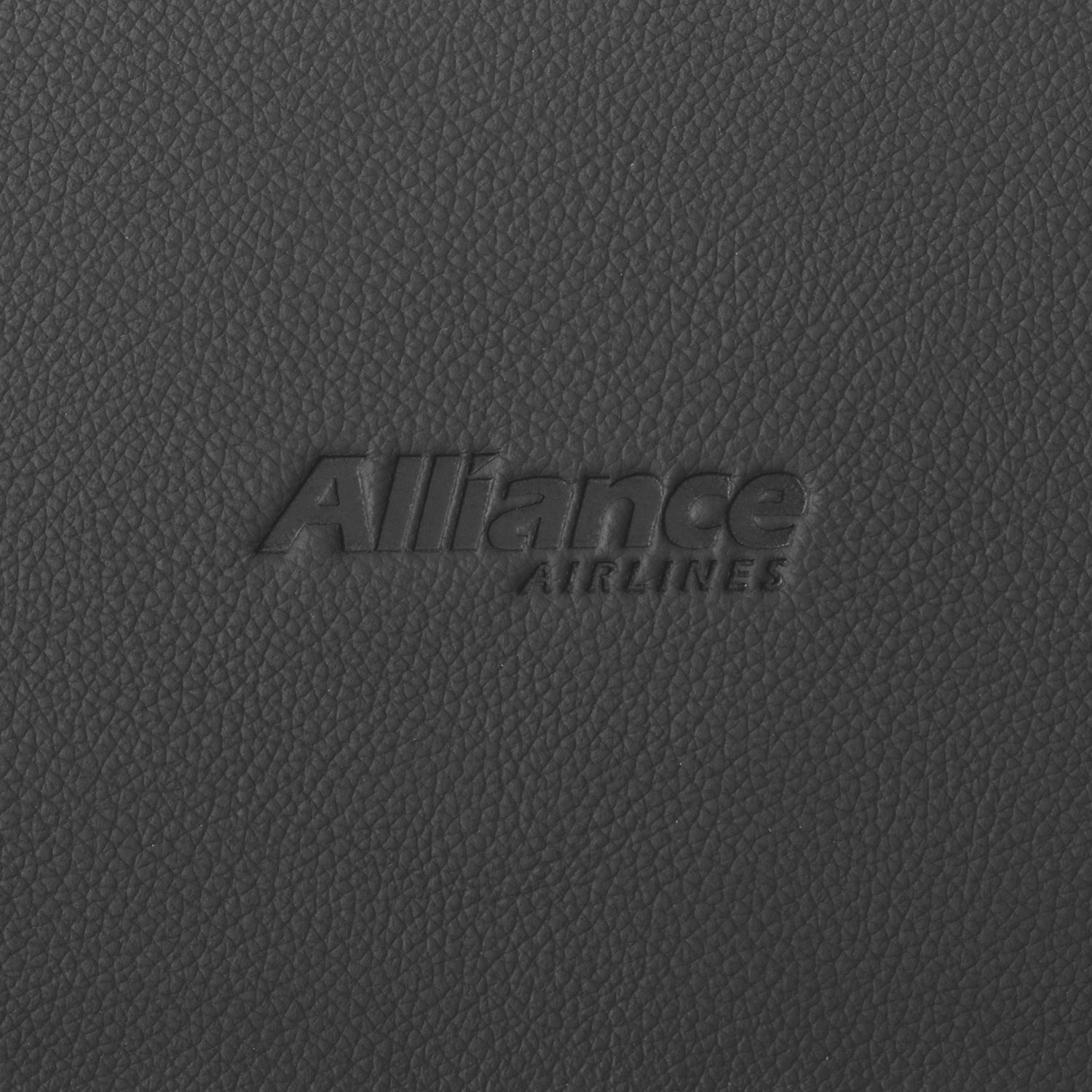
Emboss & Debossing
Embossing and debossing on airline dress covers are techniques used to create raised or recessed designs on the fabric, adding a premium aesthetic and branding element to seat covers.
- Embossing raises a pattern or logo on the material surface using heat and pressure, giving a tactile, three-dimensional effect. This is often used on leather or synthetic materials to enhance visual appeal.
- Debossing presses the design into the fabric, creating a sunken effect that adds a subtle, sophisticated look.
Both methods are durable and can incorporate airline logos or custom patterns while maintaining compliance with aviation material standards.
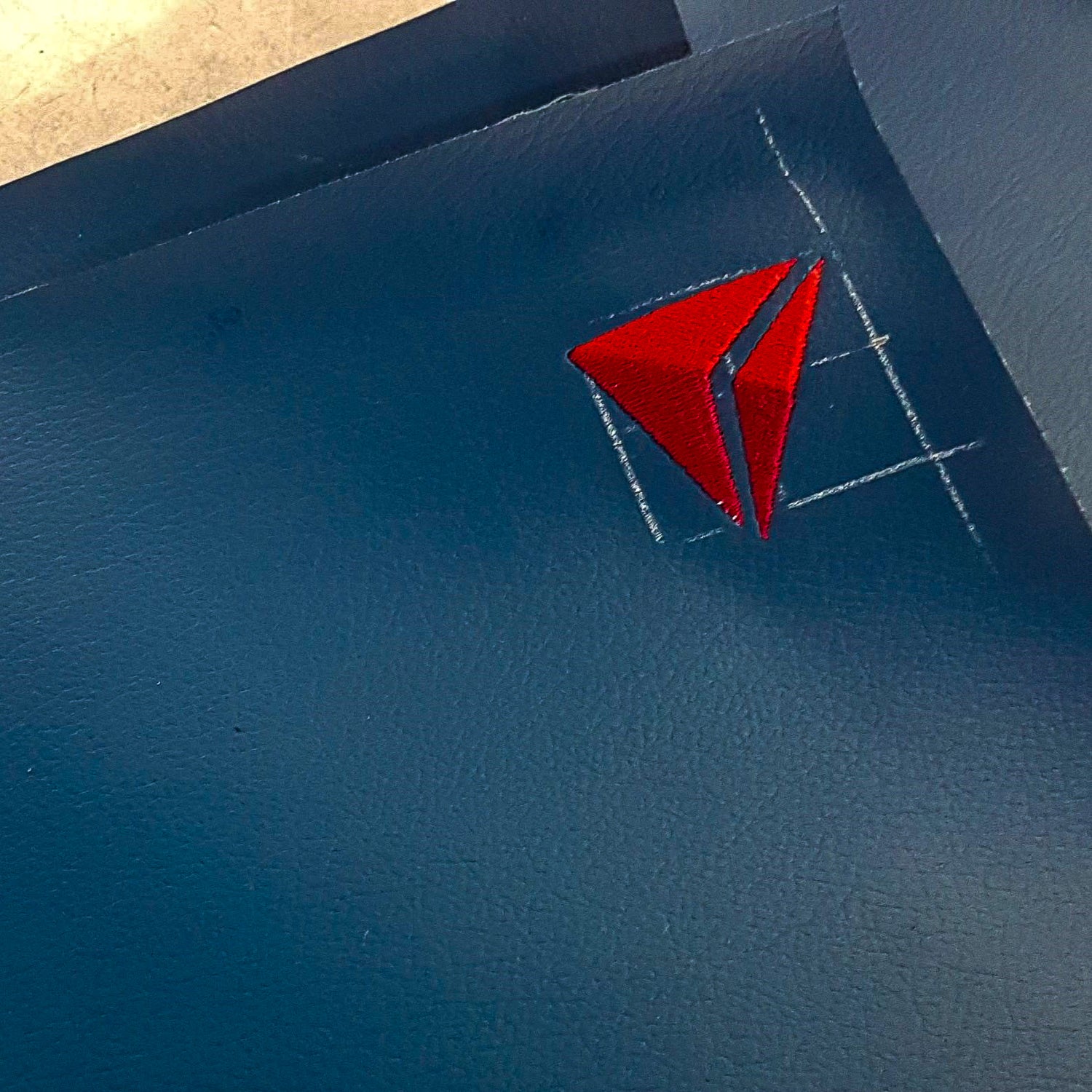
Embroidery
Embroidery on airline dress covers involves stitching logos, patterns, or decorative elements onto the fabric using computerized embroidery machines. This technique adds a premium, high-quality aesthetic while reinforcing brand identity. Embroidery is durable, resistant to wear, and can be applied to various materials, including leather and synthetic fabrics. It enhances the visual appeal of seat covers while maintaining compliance with aviation safety standards for fire resistance and durability.

Sewing
Sewing for airline dress covers is the process of stitching fabric pieces together to create durable and precisely fitted seat covers. It involves specialized industrial sewing machines that ensure strong, consistent seams capable of withstanding high usage in aviation environments. Different stitching techniques, such as double stitching or reinforced seams, enhance durability and prevent fraying. High-quality sewing is essential for maintaining the structural integrity, aesthetic appeal, and comfort of airline seat covers while complying with aviation safety and durability standards.
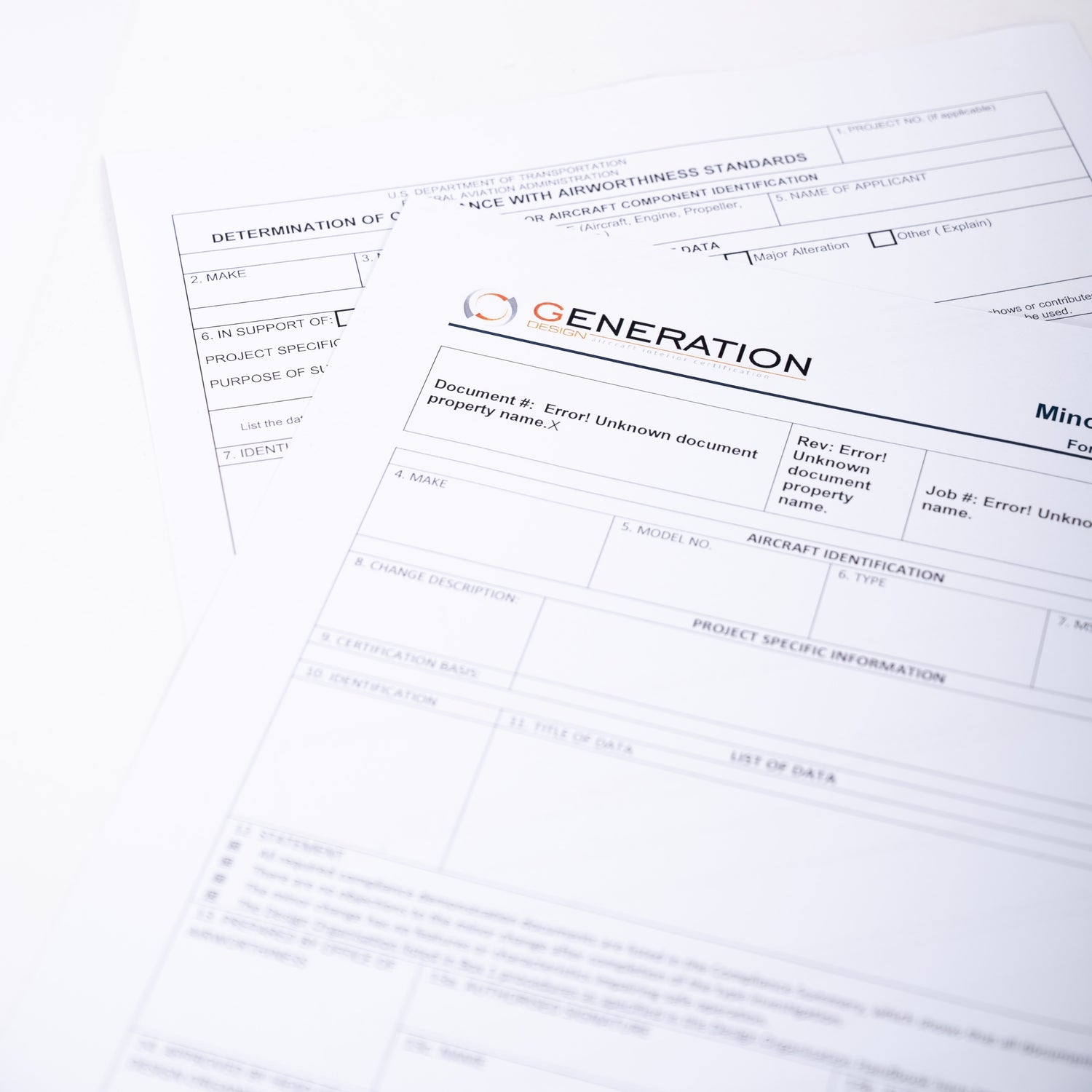
Certification Paths
EASA POA
EASA DOA
Testing
Dual Release
Installation Support
Generation Global arranges all testing and approved certification data for the refurbishment work. We often arrange validation of approvals with other aviation authorities as required. The parts are delivered with an EASA Form 1 for immediate installation.
Lets Start a Conversation
Discover more about our Airline Interiors by speaking to one of our team members today