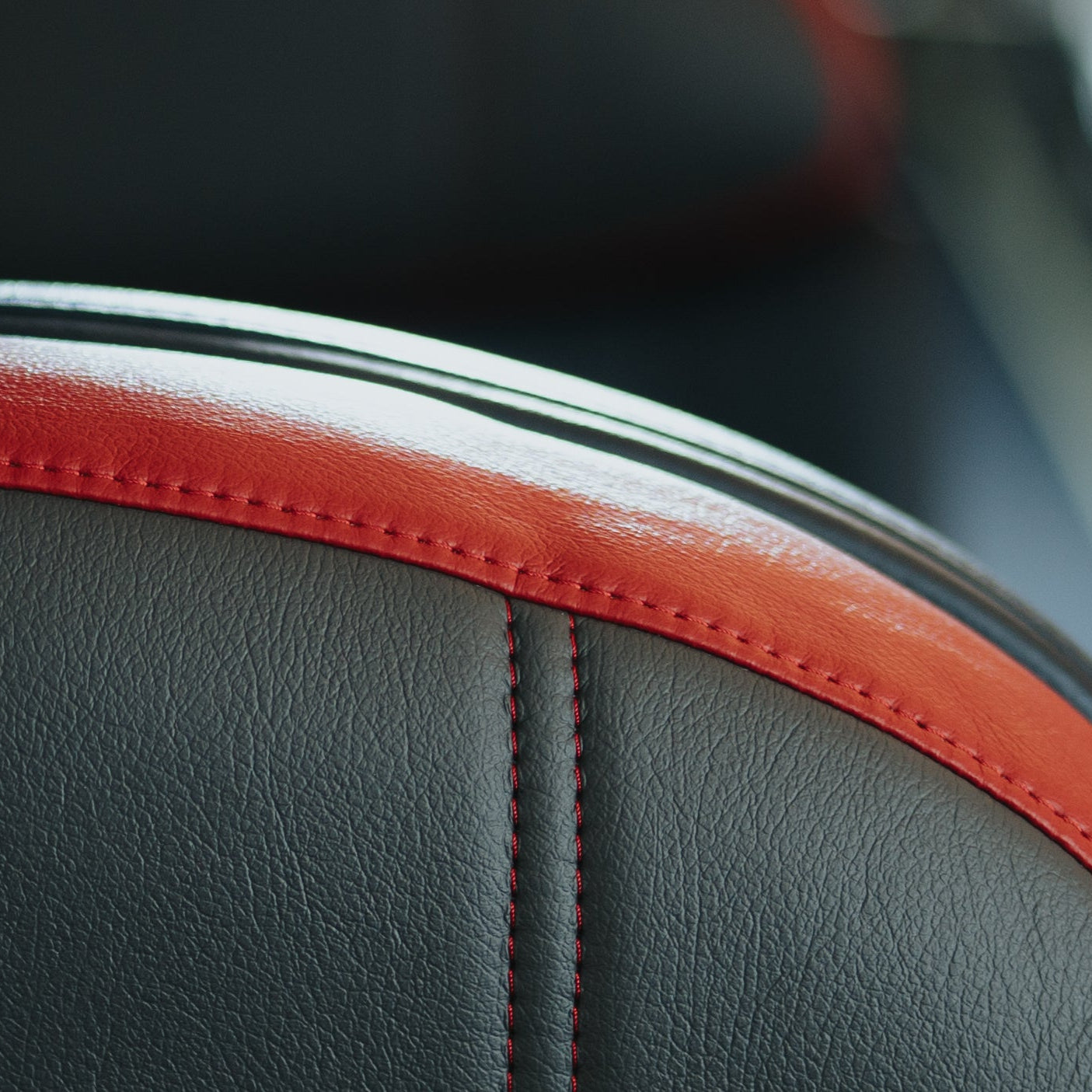
Why Generation Global?
Generation Global stands out by providing turn-key solutions that make changing your aircraft interior seamless and hassle-free. Our reputation for fast and efficient certification ensures your projects are completed on time and on spec.
Choose Generation Global for comprehensive, ready-to-use solutions with global reach.
Cushion Production
Generation Global design seat cushions to meet strict flammability, weight and comfort requirements.
Seat cushions are manufactured using modern in-house converting equipment.
A full range of foams are held in stock on site for immediate cutting, assembly, fire blocking and dispatch.
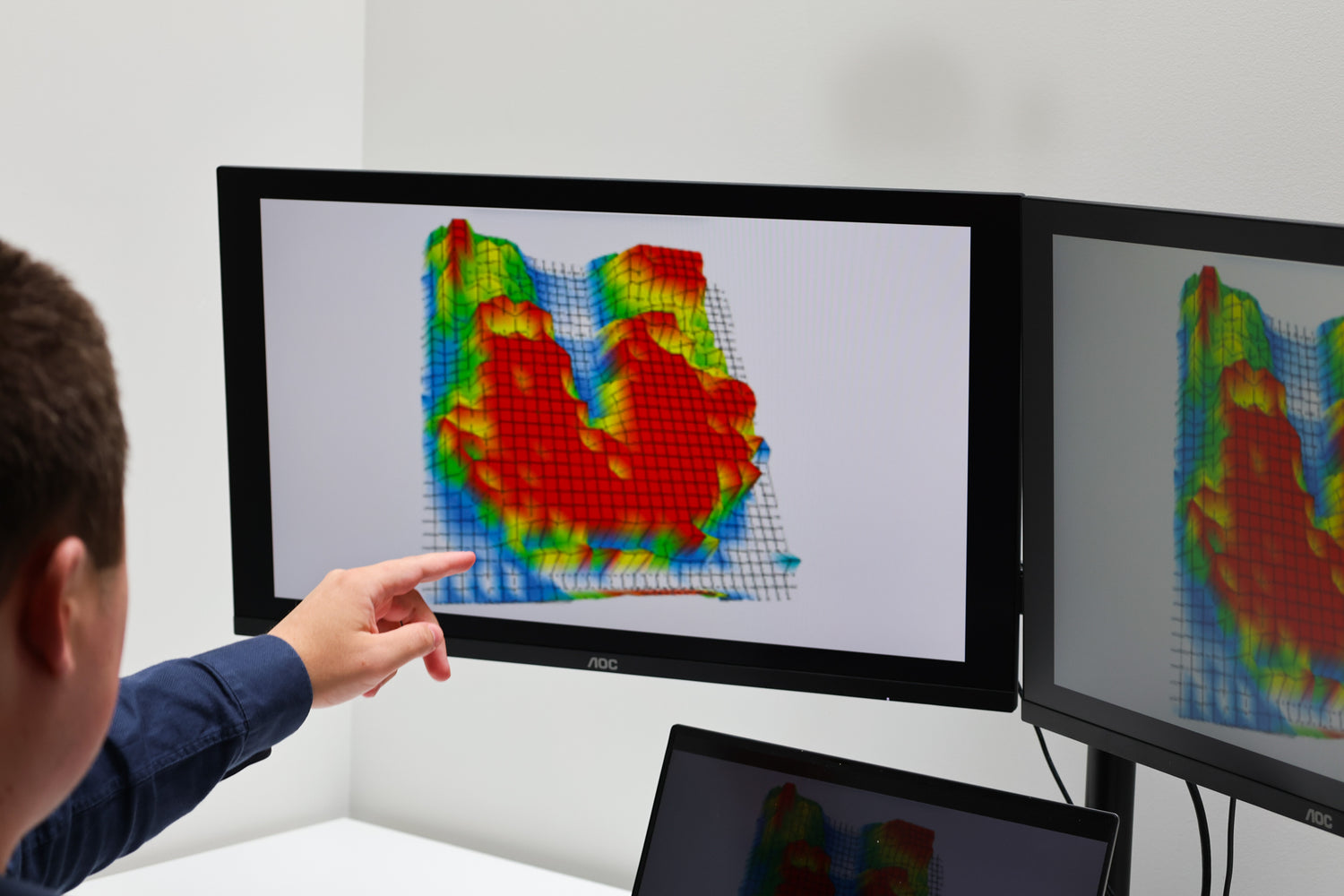
3D Renders & Modelling
3D modeling helps in refining designs, optimizing comfort, and simulating real-world usage, while rendering provides realistic previews for presentations and approvals. This technology streamlines the development process, reduces prototyping costs, and ensures precise manufacturing of airline seat cushions that align with brand and safety standards.
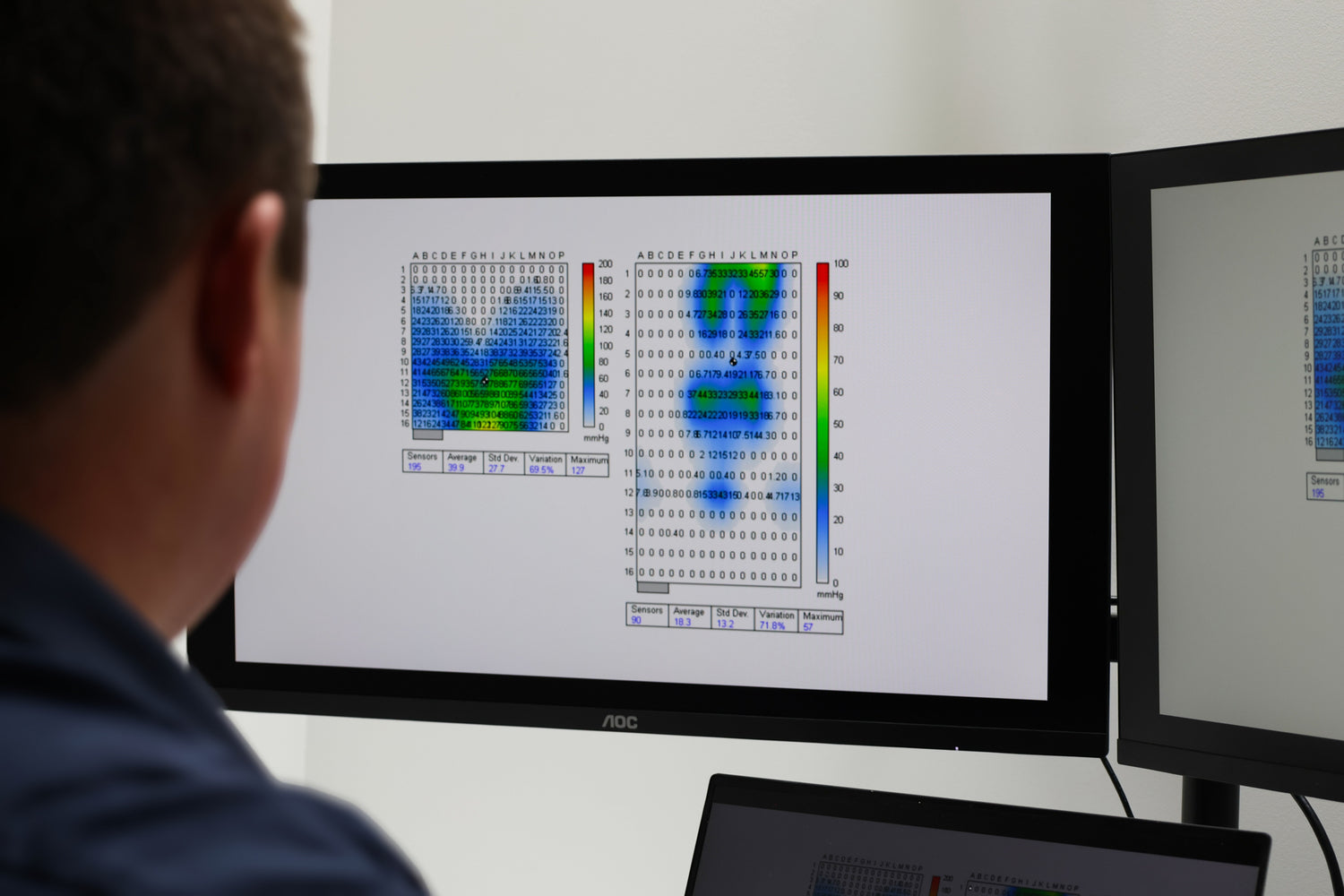
Pressure Mapping
Pressure mapping for airline seat cushions is a process that uses specialized sensors to measure and visualize the distribution of pressure across the surface of the seat cushion. By mapping how pressure is applied when a passenger sits, this technology helps designers optimize the cushionβs ergonomic design for maximum comfort and support.
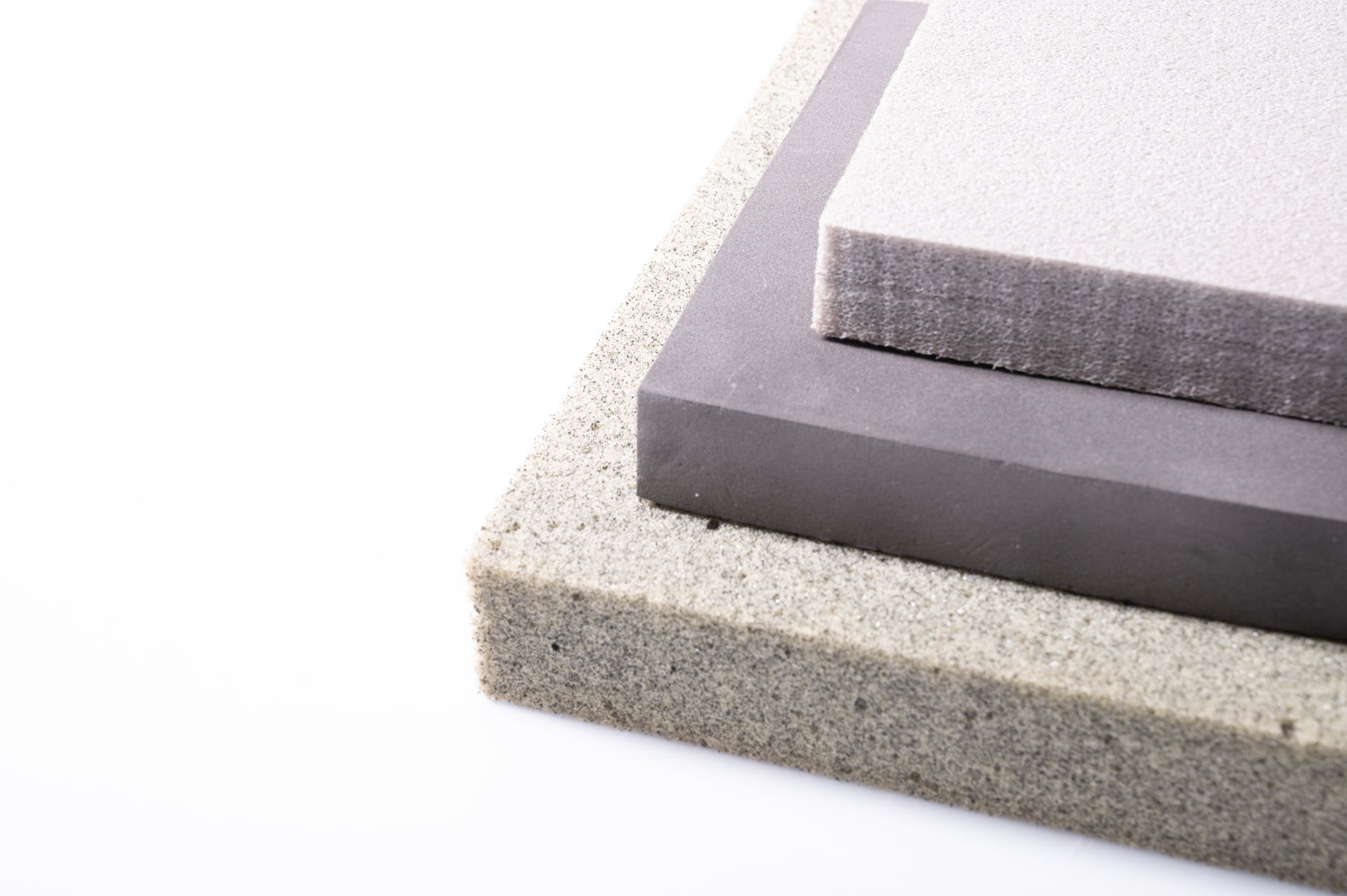
Foam Stock
Raw foam materials used in the production of seat cushions, designed to meet aviation industry standards for comfort, durability, and fire resistance. Different types of foam, such as high-density polyurethane, memory foam, and fire-retardant foams, are selected based on weight, resilience, and passenger comfort requirements.
Foam stock is typically cut, shaped, and layered to optimize support and pressure distribution. It must comply with FAA and EASA flammability regulations, ensuring safety while maintaining a lightweight and ergonomic design for airline seating.
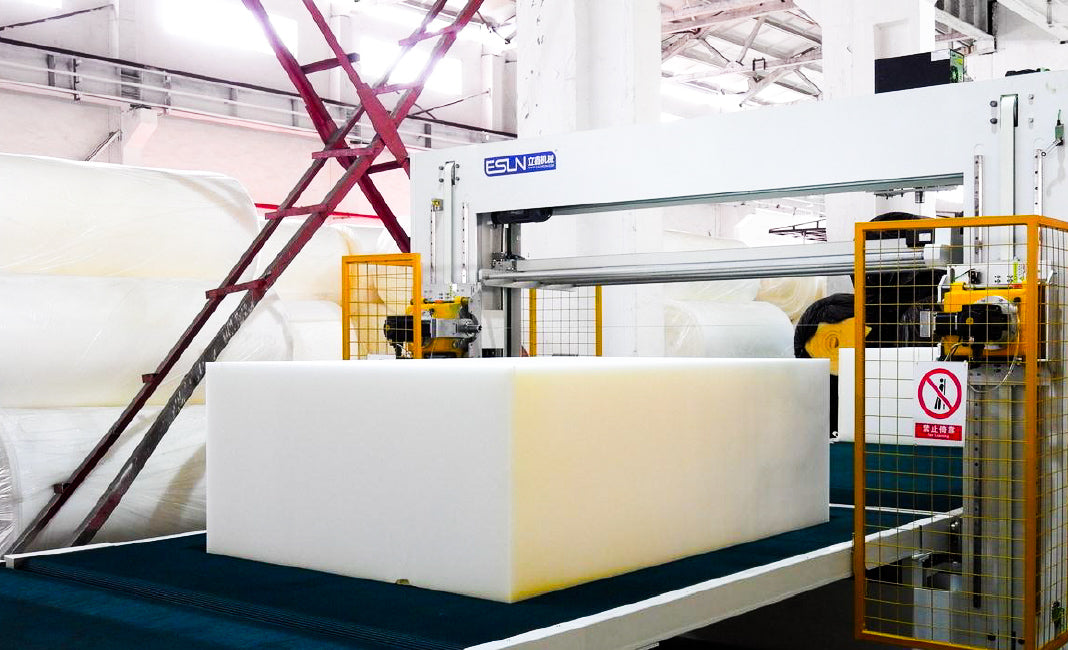
CNC Cutting
CNC cutting for airline cushions uses automated machines controlled by computer programs to precisely cut foam materials into specific shapes and sizes. This process ensures high accuracy and consistency, enabling the production of cushions with optimal support and comfort. CNC cutting can handle complex designs and intricate patterns, such as contours or grooves, to enhance ergonomics and fit within the aircraft seat structure. It also reduces material waste and increases efficiency, making it ideal for large-scale cushion production. Additionally, CNC cutting ensures compliance with safety standards, including fire resistance, for airline seating.

Parts Production
The production process may include techniques like CNC cutting, injection molding, sewing, and lamination to create each piece with the required specifications for comfort, durability, and safety. The components are then assembled to form the finished airline seat cushion, ensuring they meet aviation standards for fire resistance, ergonomics, and overall performance. Parts production plays a key role in streamlining manufacturing and ensuring consistency across large-scale seating orders.
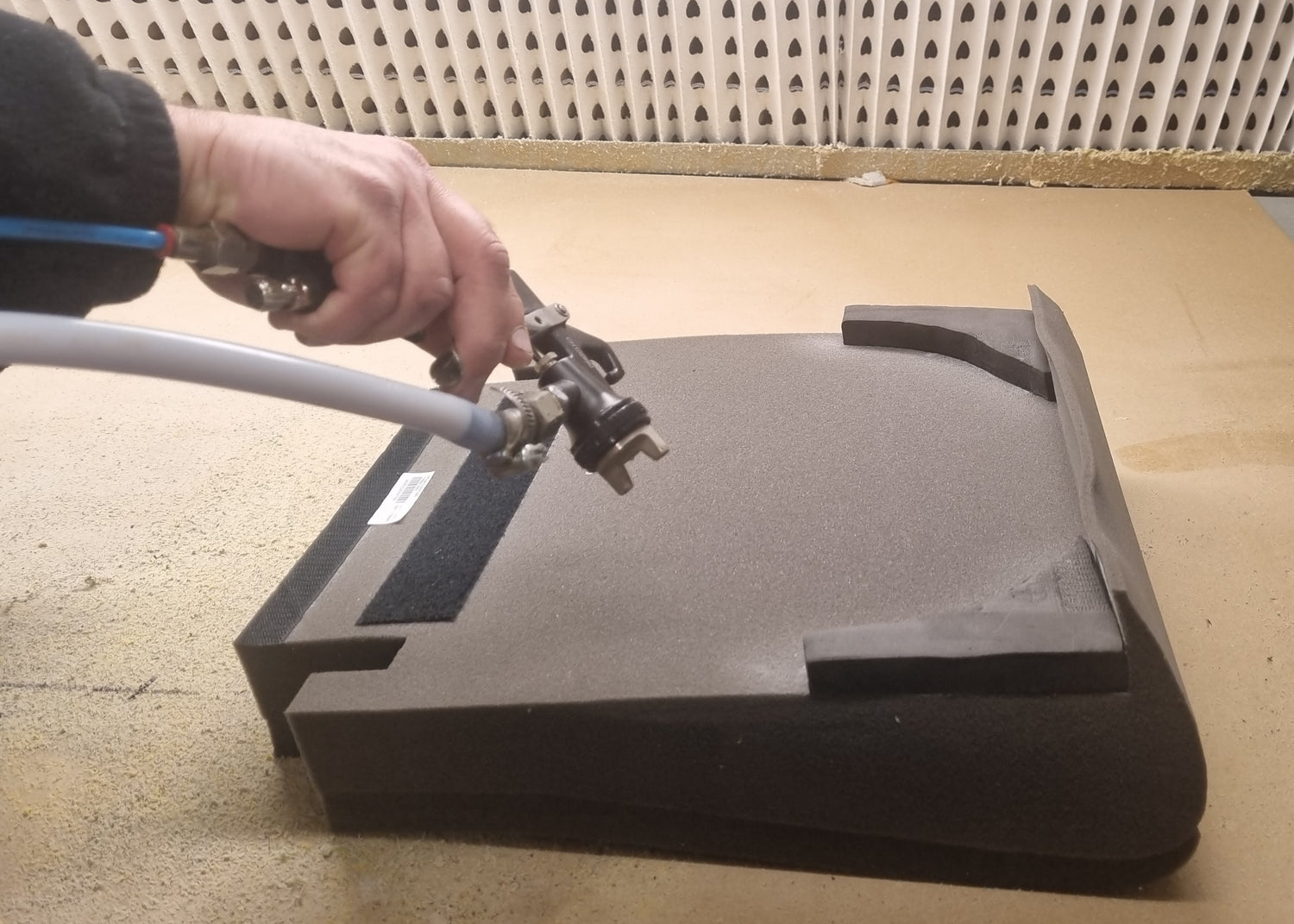
Parts Assembly
Parts assembly for airline cushions involves the process of putting together the individual components, such as foam layers, fabric covers, seat pans, and other cushioning materials, to create the final seat cushion product.
The parts are carefully assembled to ensure that the seat cushions meet all relevant aviation safety standards, including fire resistance, durability, and comfort. The goal is to deliver a high-quality, reliable product that fits perfectly within the airlineβs seating configuration.
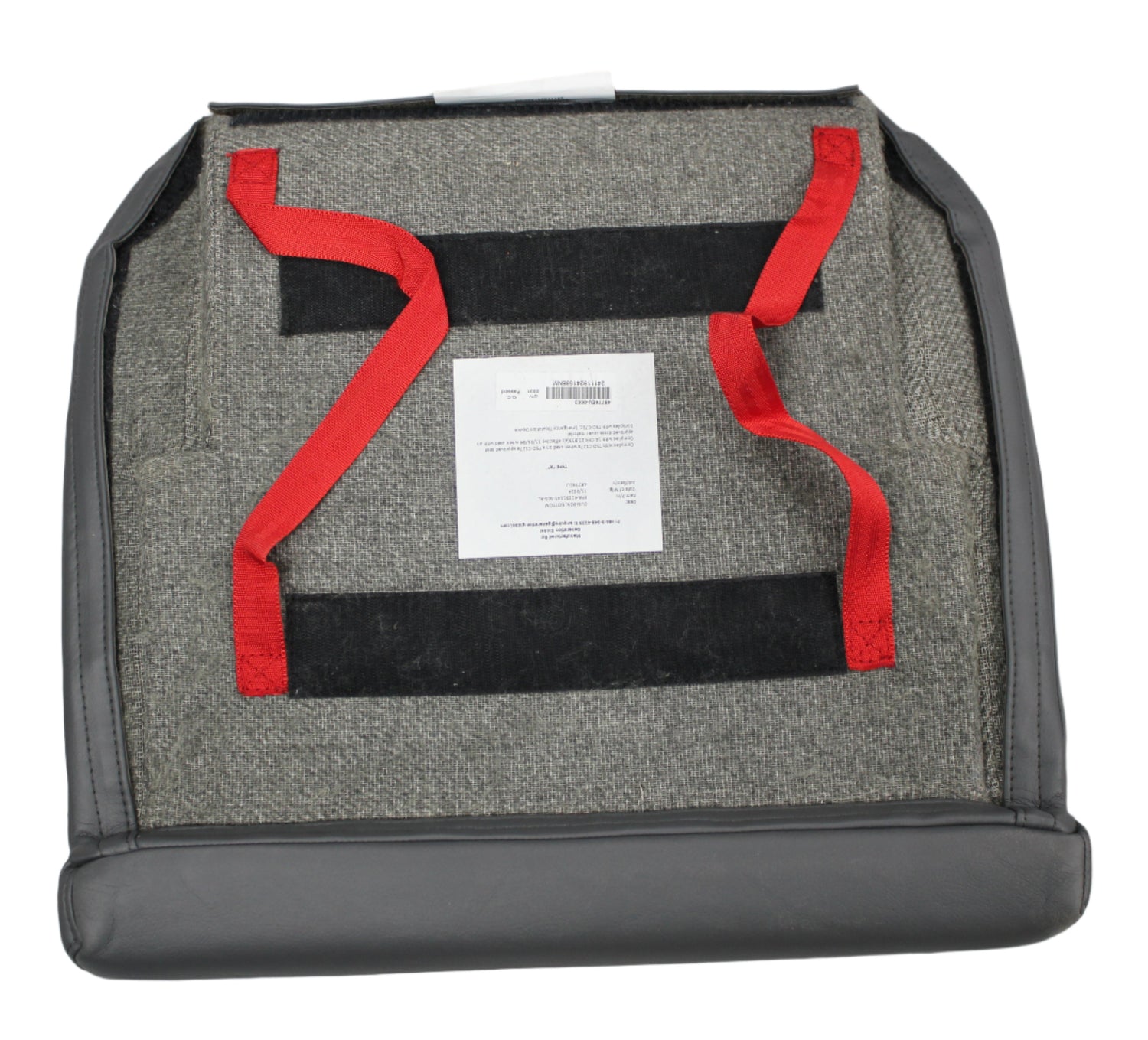
Fireblock Layers
The fireblock layer serves as a barrier to slow or prevent the spread of flames, helping to protect passengers in the event of an emergency. These layers are usually placed between the foam and fabric cover, ensuring that the cushion remains compliant with FAA (Federal Aviation Administration) and EASA (European Union Aviation Safety Agency) fire safety regulations. Fireblock layers play a critical role in maintaining the safety and performance of airline seat cushions while not compromising on comfort or durability.
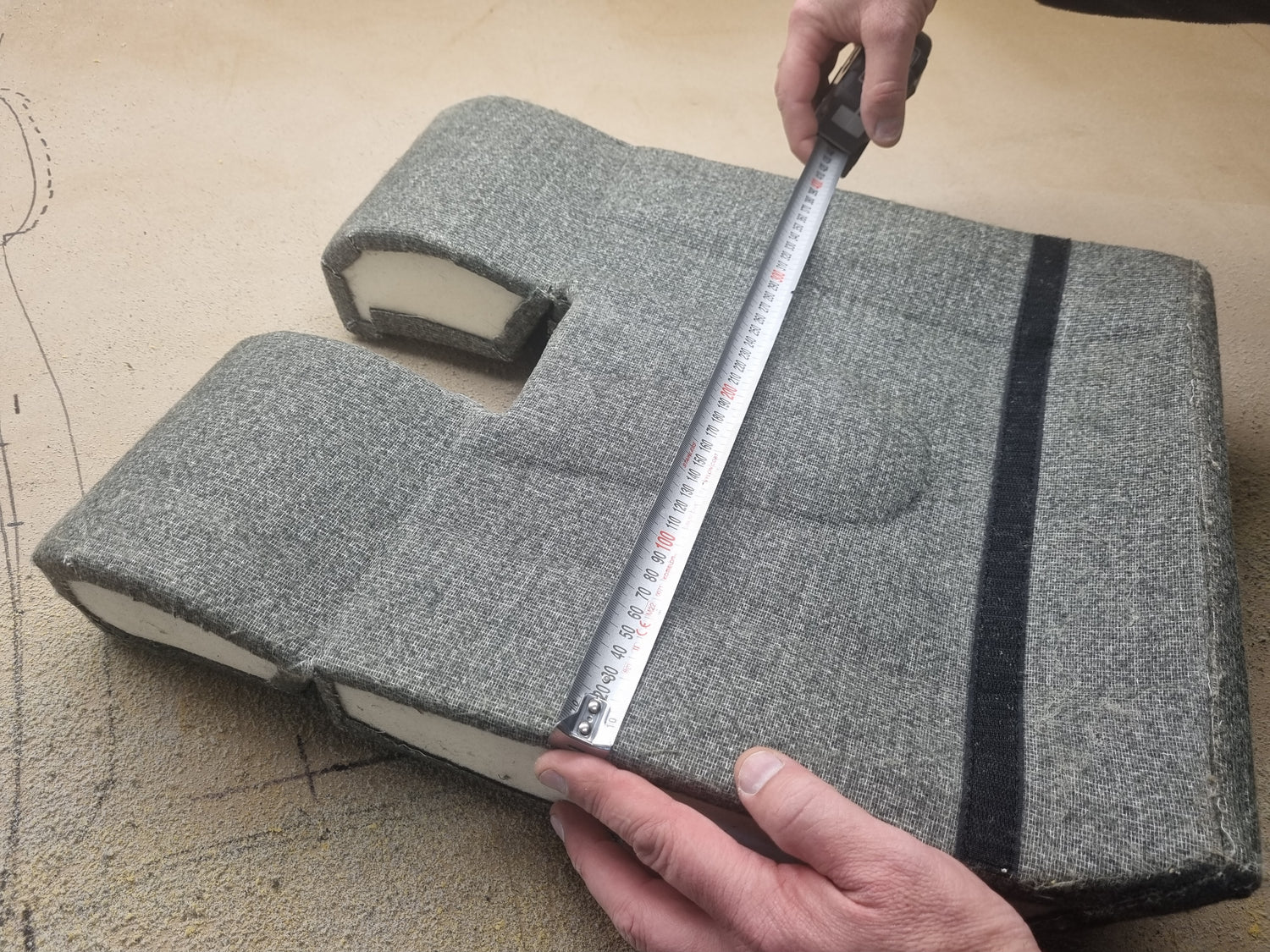
Quality Control
Quality control in the production of airline seat cushions ensures that all components and finished products meet the required standards for comfort, safety, and durability.
This rigorous quality control process ensures that the seat cushions are not only comfortable for passengers but also meet the high standards required in aviation for safety and performance.
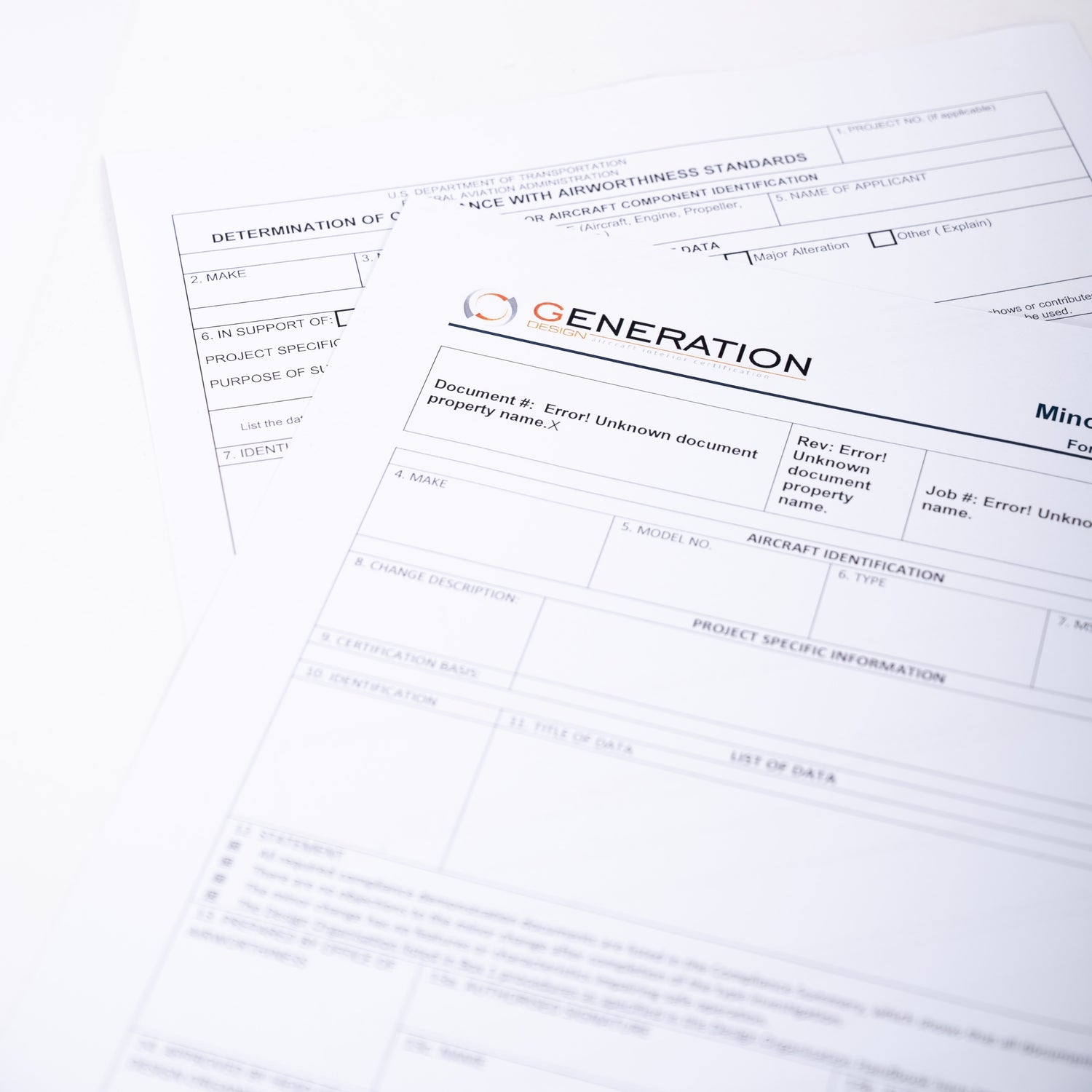
Certification Paths
EASA POA
EASA DOA
Testing
Dual Release
Installation Support
Generation Global arranges all testing and approved certification data for the refurbishment work. We often arrange validation of approvals with other aviation authorities as required. The parts are delivered with an EASA Form 1 for immediate installation.
Lets Start a Conversation
Discover more about our Airline Interiors by speaking to one of our team members today